Printed circuit board (PCB) surface finish is an important final step in PCB manufacturing that protects the underlying copper against oxidation and enhances the wetting ability of contact areas for soldering. Selecting the appropriate surface finish is crucial to ensure proper soldering and increase the PCB's storability. Which surface finish do you usually pick?
Two popular PCB surface finishes are Hot Air Leveling (HAL) lead-free and Chemical Gold (ENIG). Let's compare the advantages and disadvantages of both.

By using a microscope, we can easily notice visible differences between the two technologies. It's important not to solely consider the price when selecting a PCB surface finish, as it could result in unpleasant surprises during manufacturing, such as missing solder joints between pads and ICs.
HAL lead-free is a well-proven method that applies tin as the circuit board surface. It offers good solderability and reflow properties and is suitable for standard Surface Mount Device (SMD) applications. It is also available at the PCB manufacturers in pool-service for a low price, making it a more economical option for large production runs.
However, HAL lead-free has some weaknesses for fine-pitch applications, which other surface should be preferred. The non-planar pads are also a disadvantage of HAL lead-free, which makes it less suitable for high-density components. Another drawback of HAL lead-free is that it is not RoHS-compliant, which limits its use in some industries.

HAL leadfree surface have "bumpy" pads. The thickness of the coating is changing between pads which is not the best for fine pitched packages.
On the other hand, Chemical Gold (ENIG), also known as immersion gold, is an extremely flat surface finish with very good oxidation properties. It is perfectly suited for fine-pitch and bonding (aluminium wire) applications, as well as SMD. ENIG has excellent wetting characteristics and good storability. Like HAL lead-free, it is available in pool-service at a lower price, making it an economical choice for larger production runs.
One of the significant advantages of ENIG is its absolute flatness, making it an ideal choice for high-density components. The flat surface also ensures that there is no solder bridging between pads, which is a common issue with non-planar surfaces. However, ENIG does have a slightly higher cost compared to HAL lead-free.

In conclusion, when it comes to selecting a PCB surface finish, it is essential to consider the final product or the designated point of use of the final product. While HAL lead-free is a good option for standard SMD applications, Chemical Gold (ENIG) is more suitable for high-density components and fine-pitch applications. Ultimately, the selection of surface finish depends on the specific requirements of the application, and the desired balance between performance and cost.
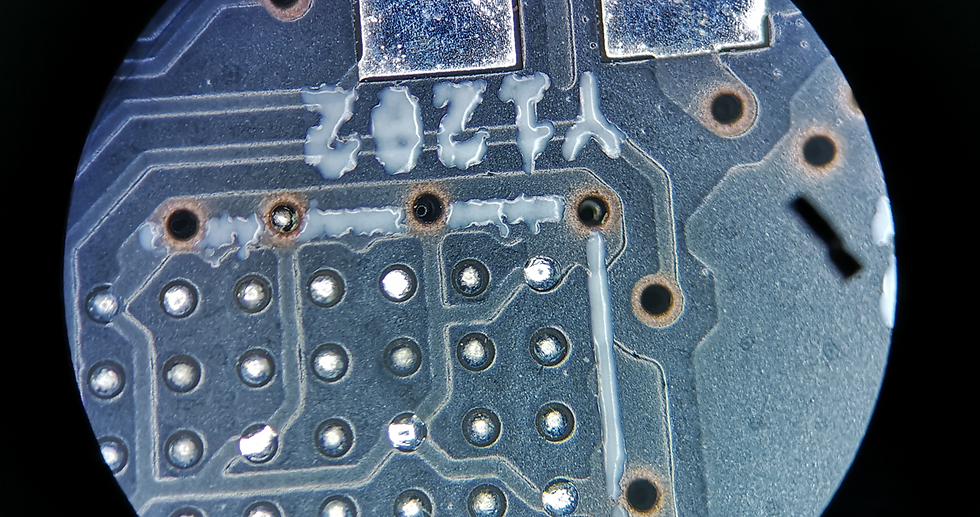
Integrated circuits, particularly those with fine pitch BGA packages like FPGAs, often come in a pre-balled state, meaning that they already have solder balls on them when you order it from your favorit electronics supplier. However, this is also a no-go for HAL lead-free technology, because the surface will be uneven and you will have two kind of solder material which never a good idea to melt.
More info:
Comentários